What is Cross-Docking?
In the fast-paced world of logistics, where speed and efficiency are of utmost importance, cross-docking remains an underutilized mechanism to move goods through the middle mile. In basic form, cross-docking involves directly transferring groups of finished goods through a facility without the need for individual package level sortation or storage. Some liken it to a relay race, where the baton smoothly passes from one runner to the next, optimizing each leg for maximum speed and precision.
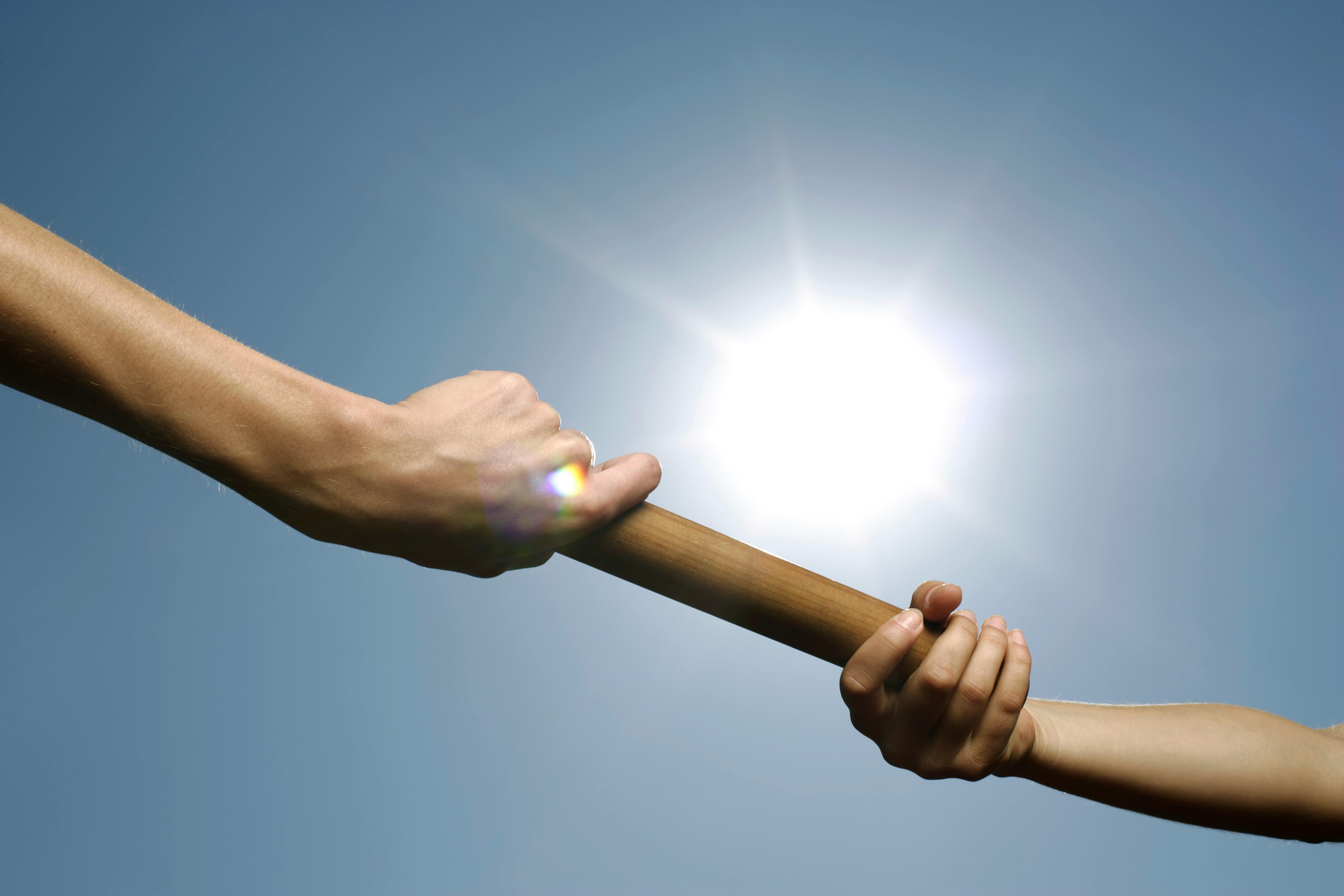
Different Types of Cross-Docking
Cross-docking can take various forms, each tailored to specific business needs and industries.
1. Transportation Cross-Docking
Transportation cross-docking generally focuses on optimizing the transportation components of the supply chain. Goods that unloaded from incoming trucks can be quickly loaded onto outbound vehicles without the need for costly and time consuming piece level sortation. This method increases asset utilization (facilities and transport), reduces transit times, lowers shipping costs, and enhances the overall efficiency of goods distribution, particularly for long-haul transportation routes.
2. Retail Cross-Docking
In the retail sector, where speed is paramount, retail cross-docking ensures seamless product flow from suppliers to retail shelves. Goods are presorted into containers destined for individual stores or specific departments within stores. This pre-segregation minimizes the need for warehousing while reducing defects and theft. Retailers are empowered to maintain lean inventories, respond swiftly to changing customer demands, and keep shelves stocked.
3. Manufacturing Cross-Docking
Manufacturing cross-docking supports efficient production processes. It involves delivering raw materials and components directly to the manufacturing line, minimizing inventory holding and handling. By ensuring an activity area or assembly point receives precisely what they need, precisely when they need it, enables production schedules to be optimized and costs reduced.
4. Distributor Cross-Docking
Distributor cross-docking streamlines the distribution process by consolidating products from multiple suppliers into a single shipment. This approach reduces storage costs and expedites the delivery of goods to retailers or end customers. Distributors act as intermediaries, swiftly moving products through their facilities, ultimately benefiting both suppliers and customers.
Benefits of Cross-Docking
1. Improved Efficiency & Faster Delivery Times
One of the most meaningful advantages of cross-docking is its ability to streamline the movement of goods, resulting in faster delivery times. By eliminating the need for duplicative handling and touches, products move swiftly from suppliers to end customers or retailers. This speed can be revolutionary, particularly in industries where timeliness is a competitive advantage. With cross-docking, goods reach their destinations faster and with fewer instances of defects or damage.
2. Reduced Warehousing Costs
Traditional package level or piece level sortation activities often create bottlenecks and entail costly material handling and operational expenses. Cross-docking slashes these costs by reducing or eliminating the need for redundant activities. With fewer bottle-necks, companies save on rental or leasing costs, labor, and inventory carrying costs, freeing up resources for other critical business activities.
3. Better Inventory Management
Cross-docking's lean approach to inventory management ensures businesses maintain the optimal amount of stock. This minimizes the risk of overstocking or understocking, allowing companies to operate more efficiently. Additionally, real-time inventory tracking and management systems keep a close watch on stock levels, making it easier to respond to fluctuations in demand.
4. Enhanced Customer Satisfaction
In today's era of instant gratification, cross-docking plays a vital role in helping organizations to exceed customer expectations. Faster delivery times and reduced order fulfillment errors result in higher customer satisfaction levels. Businesses that adopt cross-docking are better positioned to meet the demands of today's discerning consumers, fostering loyalty and repeat business.
Key Components Inside a Cross-Docking Facility
Cross-docking facilities serve as nerve centers for efficient supply chain operations. Several key components work together harmoniously to ensure seamless goods flow.
1. Receiving Area
At the heart of a cross-docking facility lies the receiving area. This is where incoming shipments from suppliers or manufacturers are unloaded and carefully inspected for quality and accuracy. Having a well designed operator tool allows for accurate tracking while providing clear instructions to the user regarding next actions to take.
2. Sorting & Consolidation Area
After goods are received, they are moved to the consolidation area, sometimes referred to as a staging area. Here, items are grouped based on their destinations or intended routes. Efficient staging ensures that containers of goods are quickly matched with outgoing loads optimizing the speed of the cross-docking process.
3. Storage (Temporary)
While the goal of cross-docking is to minimize storage time, some facilities have a temporary storage area for goods that require minor adjustments or repackaging before they can be loaded onto outbound vehicles. Another use case is when containers need to be staged for short periods of time to meet day-definite delivery requirements. This temporary storage is essential for ensuring the readiness and correct timing of products for their next journey.
4. Loading Docks
Loading docks are the final stop for goods inside a cross-docking facility. Here, products are loaded onto outbound vehicles, such as trucks or trailers. These docks are equipped with specialized equipment like forklifts, conveyor systems, and loading bays to facilitate swift and organized loading.
5. Technology Infrastructure
Technology plays a critical role in modern cross-docking facilities. Sortation Software and certain Warehouse Management Systems (WMS) provide real-time tracking of inventory and shipments. Best in class technology allows real-time updates to instructions being provided to warehouse staff.
Challenges & Considerations in Cross-Docking
While cross-docking offers significant benefits, it also comes with its set of challenges. Understanding these challenges is crucial for successful implementation.
1. Synchronization
Cross-docking works best when precise coordination exists among suppliers, carriers, and the cross-docking facility. Delays or miscommunication can lead to disruptions. Real-time communication tools and streamlined processes are essential to address this issue.
2. Quality Control
Ensuring the quality of goods during rapid transfers can be challenging. Implementing quality checks and inspections at key points in the cross-docking process helps prevent damaged or subpar products from reaching customers.
3. Infrastructure and Space
Facility layout and space constraints can limit the scale of cross-docking operations. Investing in facility optimization and adequate space planning is necessary for accommodating growing demand.
4. Labor Efficiency
Efficiently managing labor during peak times can be tricky. Cross-docking requires skilled personnel and proper training to handle the fast-paced environment effectively.
The Future of Cross-Docking
As technology continues to advance, the future of cross-docking holds even greater promise. Automation and artificial intelligence are transforming the logistics landscape, offering opportunities for increased efficiency and cost savings. Robots and automated systems can streamline processes within a cross-docking facility, further optimizing the flow of goods. Additionally, advanced analytics and predictive modeling can enhance demand forecasting and inventory management, enabling businesses to make data-driven decisions.